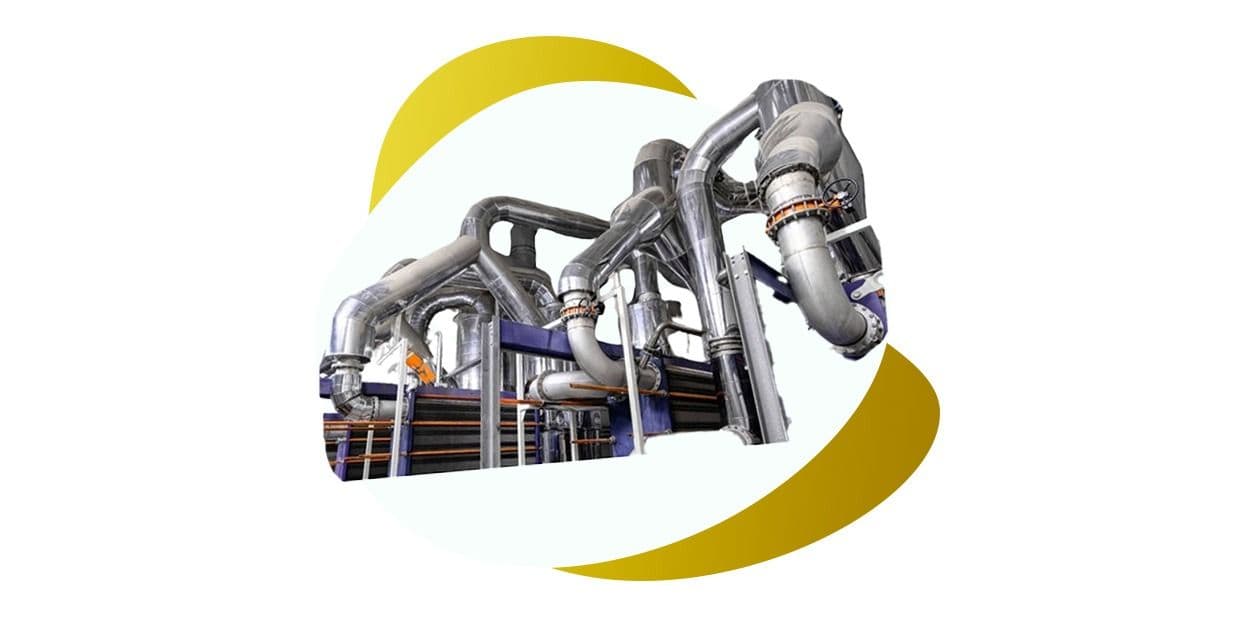
Discover how chilled water piping systems can slash your energy bills while keeping your building cool and comfortable.
A chilled water piping system is a crucial component in modern HVAC setups, especially for large-scale applications like commercial buildings, hospitals, and data centers. These systems work by circulating chilled water through insulated pipes to absorb heat from the air, providing efficient and consistent cooling. Unlike traditional air conditioning methods, chilled water systems offer superior energy efficiency, which can lead to significant cost savings over time. In this guide, we’ll explore the ins and outs of chilled water piping systems, from their basic components to advanced maintenance tips, helping you understand why they’re the go-to choice for many facility managers and engineers.
What Is Chilled Water Piping System?
A chilled water piping system is a type of insulated pipe that supplies and returns chilled water to and from the chiller and the cooling units. It is extensively applied in commercial buildings, hospitals, manufacturing facilities, and other large scale HVAC systems for effective cooling.
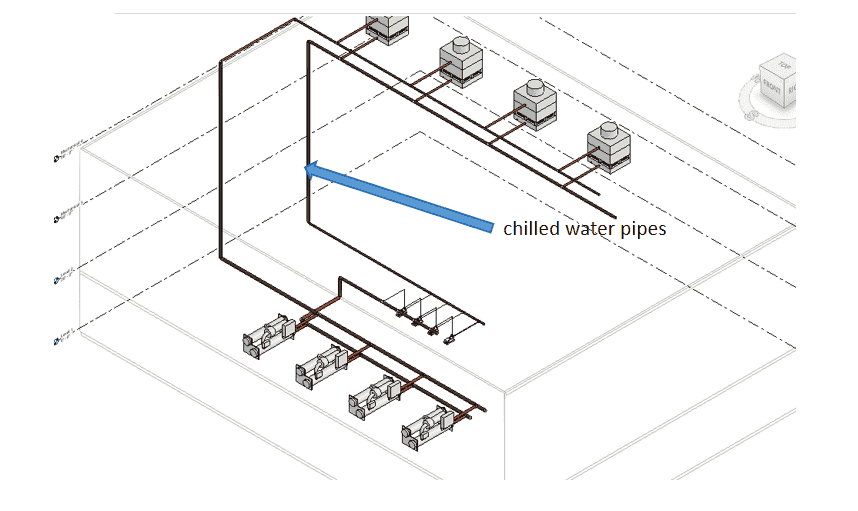
What Are The Functions Of The Chilled Water Piping System?
The System is a Closed-Loop Cycle:
- The Chiller cools water to a certain temperature, usually between 40 and 50 F (4 to 10 C).
- A Pump is used to circulate the chilled water through various insulated pipes.
- The cooled water now picks up heat from air handling units (AHUs) and fan coil units (FCUs) or any other process cooling system.
- The water that is returned is now warmed and goes back to the chiller. The cooling cycle is repeated.
Components of a Chilled Water Piping System
1. Chiller
- This is the part of the water chiller that is responsible for cooling the water by means of refrigerants.
- A chiller can be an air cooled or water cooled chiller.
2. Pipes
- Constructing materials are usually steel, copper or PEX.
- The components must be insulated to prevent absorption of excess heat and loss of energy.
3. Pumps
- These are devices that help move chilled water within a certain system.
- The layout of the system determines if the pump is primary, secondary, or tertiary.
4. Control Valves
- These are devices that control the water flow for a certain purpose.
- Examples are manual, motorized, and PICV (pressure independent control valves).
5. Expansion Tanks
- Absorbers and water pressure changes are managed in a way that handles temperature changes.
6. Cooling Coils
- Cooling coils with chilled water have the capability to absorb the heat from air and transfer it to the chilled water in the pipes.
Chilled Water Piping Systems
1. Constant Volume System
- Set rate pumps are operational.
- These systems are not very energy efficient modern day, but are simplistic and straightforward.
2. Variable Flow System
- The limit set by the user is compared to the flow rate and the system is altered to meet the limit.
- New innovative technologies suggest that this system can save and reduce costs substantially in time.
3. Primary-Secondary Loop System
- Distribution chiller has defined and isolated secondary systems with independent loops.
- It is more effective and has more flexibility.
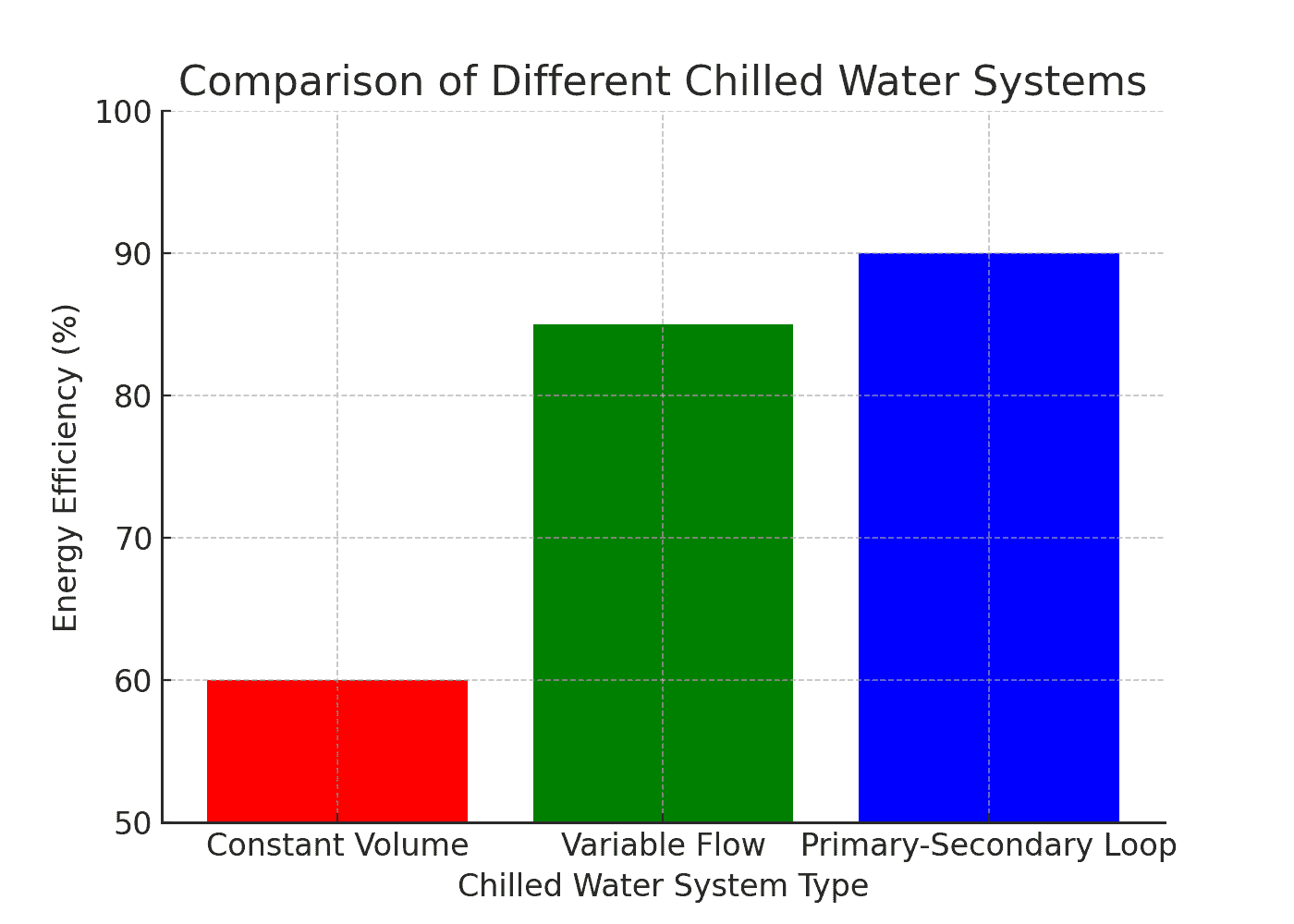
Advantages of a Chilled Water Piping System
- Savings in Operating Costs: Reduce operating costs in comparison to distinct air conditioner systems.
- Enhanced Cooling Range Accuracy: Ensures that the cooling constant and proper cooling range is always accurate.
- Easier Expansion: Determine its position in relation to the already existing structures.
- Depreciation Of The System: If the system is properly used, it can be preserved for quite some time.
- Lower Carbon Emissions: On using energy efficiently, effective energy use lowers carbon emissions.
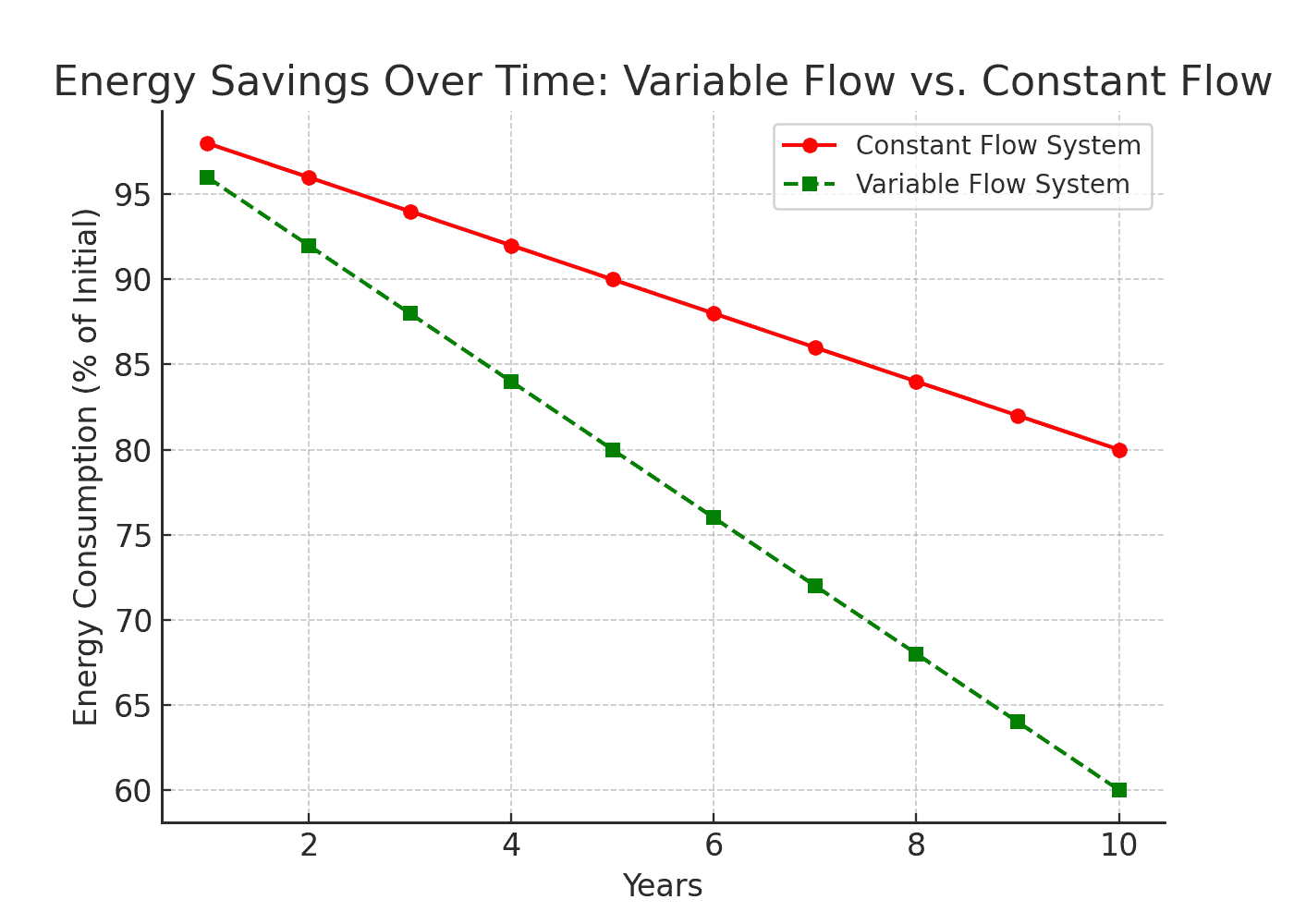
Impact on Energy Efficiency
Chilled water piping plays a significant role in the energy efficiency of HVAC systems, especially in large buildings. Proper insulation helps minimize heat gain, reducing the workload on the chiller and lowering energy use. For example, in a typical commercial building with a cooling load of 100 tons, insulating 1,000 feet of 6-inch pipe could reduce the chiller's energy use by about 5%, potentially saving around $1,155 annually at $0.10 per kW-h.
Supporting Statistics
A notable statistic is that a 1% increase in the wetness of pipe insulation can reduce its thermal efficiency by 7.5%, as confirmed by authoritative bodies like ASHRAE, the Environmental Protection Agency, and the Department of Energy. This highlights how maintaining dry insulation is vital for energy efficiency. Additionally, for a 6-inch pipe, proper insulation can reduce heat gain by 90%, from 20 BTU/h per foot to 2 BTU/h per foot over 1,000 feet.
Unexpected Detail: System-Wide Effects
Beyond energy savings, proper insulation also prevents issues like condensation, mold growth, and potential pipe damage, which can lead to costly repairs and affect system reliability—an aspect not immediately obvious but critical for long-term efficiency.
Detailed Analysis of Chilled Water Piping and Energy Efficiency
Chilled water piping is a critical component of heating, ventilation, and air conditioning (HVAC) systems, especially in large commercial and industrial settings. These systems use chilled water to cool air, and the efficiency of the piping network directly impacts the overall energy consumption of the system. This report delves into how chilled water piping affects energy efficiency, supported by statistical data and references from authoritative sources, providing a comprehensive overview for stakeholders interested in optimizing HVAC performance.
Importance of Chilled Water Piping in Energy Efficiency
Chilled water systems operate by circulating cold water through a closed loop, where the water is cooled by a chiller and then distributed to air handlers or other cooling loads. The piping network is essential for delivering this chilled water efficiently. However, if the pipes are not properly insulated, heat can be gained from the surrounding environment, increasing the temperature of the water before it reaches the load. This heat gain forces the chiller to work harder to maintain the desired supply temperature, thereby increasing energy consumption.
Research suggests that proper insulation of chilled water pipes can lead to significant energy savings, with estimates ranging from 4% to 8% of the chiller's energy consumption. This range is derived from studies and reports, such as those from ASHRAE and the National Insulation Association, which highlight the importance of minimizing heat gain to reduce the cooling load on the chiller. For instance, in a typical commercial building with a cooling load of 100 tons (1,200,000 BTU/h), insulating 1,000 feet of 6-inch pipe could reduce the chiller's energy use by approximately 5%, translating to substantial annual savings depending on electricity costs.
Statistical Data on Energy Savings
To quantify the impact, consider the following statistic from Insulation Outlook Magazine (2015), confirmed by ASHRAE, the Environmental Protection Agency, and the Department of Energy: a 1% increase in the wetness of pipe insulation can reduce its thermal efficiency by 7.5%. This reduction in efficiency means the insulation is less effective at preventing heat gain, leading to higher energy consumption by the chiller. For example, if the insulation gets wet due to condensation, its thermal resistance decreases, and the heat transfer rate can increase by approximately 8.1%, as calculated from the inverse relationship between resistance and heat transfer.
Further, case studies and models, such as those discussed in a research paper on pipe insulation for energy conservation in buildings (Pipe Insulation Model for Energy Conservation in Buildings), indicate that energy savings from proper insulation can range from 2% to 23% of the annual load across different climate zones, though these figures are context-specific and often relate to broader piping systems. For chilled water specifically, the savings are more narrowly estimated at 4% to 8%, reflecting the direct impact on chiller performance.
To illustrate, consider a hypothetical scenario: for a 6-inch pipe carrying water at 42°F in an ambient temperature of 75°F, uninsulated heat gain might be around 20 BTU/h/ft, while with 1 inch of fiberglass insulation, it drops to 2 BTU/h/ft. Over 1,000 feet, this reduces the additional cooling load from 20,000 BTU/h to 2,000 BTU/h, a 90% reduction in heat gain. If the chiller has a coefficient of performance (COP) of 4, this translates to energy savings of approximately 1,318.5 Watts continuously, or about 11,550 kW-h/year, potentially saving $1,155 annually at $0.10/kW-h, though actual savings depend on system specifics.
Factors Affecting Energy Efficiency
Several factors influence how chilled water piping affects energy efficiency:
- Insulation Quality and Thickness: The type and thickness of insulation, such as fiberglass or foam, determine its thermal resistance. Increasing thickness from 1 inch to 2 inches can further reduce heat gain, as per ASHRAE guidelines.
- Pipe Length and Diameter: Longer pipes and larger diameters increase surface area, potentially increasing heat gain if uninsulated. For instance, a 1,000-foot pipe has a larger impact than a 100-foot pipe.
- Environmental Conditions: Higher ambient temperatures and humidity levels, especially in areas near water bodies, increase the risk of condensation and heat gain, making insulation critical.
- System Design: Variable primary systems, as discussed in resources like Pumping Up Efficiency: Variable Primary Chilled Water Systems Explained, can optimize flow and reduce energy use, complementing insulation efforts.
Broader Implications and Unexpected Benefits
Beyond energy savings, proper insulation offers additional benefits that may not be immediately apparent. It prevents condensation, which can lead to mold growth and corrosion under insulation (CUI), as noted in case studies like the remediation of chilled water pipe insulation at a football stadium and convention center (Case Study: Remediating Chilled-Water Pipe Insulation at a Football Stadium and Convention Center). These issues can cause system failures and costly repairs, affecting long-term operational efficiency. Moreover, reducing energy consumption lowers greenhouse gas emissions, aligning with sustainability goals, as highlighted in guides like Guide to Chilled Water Systems and Improving Efficiency.
Challenges and Considerations
While the benefits are clear, exact energy savings depend on numerous variables, making precise quantification challenging without detailed system analysis. For instance, the chiller's COP, the temperature difference between supply and return water, and the insulation's condition over time all play roles. Additionally, in high-humidity environments, ensuring insulation remains dry is crucial, as wetness can negate efficiency gains, as evidenced by the 7.5% thermal efficiency drop with 1% wetness.
Tips to Follow While Developing a Chilled Water Piping System Design
1. Make Sure to Use High-Quality Insulation
Not sufficiently insulating will lead to energy loss and condensation moisture build up. Some common types are polystyrene, polyurethane foam, fiberglass and elastomeric foam.
2. Changes In Selection Of Pipe Has Its Effects
Pipes which are oversized have an expensive installation price while undersized ones have excess pressure drops which can be too much. Only trained personnel should be given the authority to ascertain the dimensions - Cooling capacity calculations must be supplied.
3. Advanced Pumps Should Be Deployed for More Optimized Systems
In modern systems, variable-speed pumps should be deployed. The energy consumption is optimized due to the fact that these pumps can increase or decrease their flow rates based on demand.
4. Combination of Automatic Air Eliminators with Air Vents
Systems such as these achieve and control pressurized balance which is vital to increase productivity in the system as a whole.
5. Use of Non-Corrosive Materials
I node may be referred to as coating steel pipes with anti-corrosive alloy, so for better longevity of the system, anti-corrosive coatings should be applied, along with the use of stainless steel pipes.
Chilled Piping Systems: Best Practices for Maintenance
1. Routine Maintenance Checkups
Set a specific timeframe of not more than six months as the interval to check your piping insulation for any leaks, signs of corrosion, or damage.
2. Water Quality Monitoring
Scaling, corrosion, and microbial activity stem from poor water quality. Proper compounds must be administered to guarantee the system’s integrity.
3. Active Water Pump Monitoring
Bring accurate measures of flow rate, head pressure, and other vital traits in sufficient amounts to ensure proper functionality.
4. Control Valve Adjustments
Neglected control valves may lead to waste of cooling capacity. Regular care and adjustments should be made to keep them functioning appropriately.
5. Performance System Records Keeping
Check the readings for pressure and temperature as well as the maintenance logs to try and nip problems in the bud, before they become too serious.
Most Frequent Problems and Their Solutions
1. Deficiencies in Pipe Insulation Maintenance
– Apply closed cell foam insulating pipes to preserve energy and prevent moisture buildup.
2. Air within the Heating/Piping System
– Implement air vents along with automatic air eliminators into the design for enhanced energy savings.
3. Leakages and Corrosion of Pipes
– Use failure-based maintenance practices and corrosion-resistant composite materials to avoid issues.
Frequently Asked Questions
Q1: What material do you recommend for chilled water pipes?
A: Steel, copper, and PEX are popular materials. PEX is often favored due to its lower cost and excellent thermal conductivity.
Q2: How do I control condensation on chilled water pipes?
A: The addition of a vapor barrier combined with insulation wraps such as fiberglass or elastomeric foam should do the trick.
Q3: How often should a chilled water system be maintained?
A: Quarterly inspections and an annual system checkup will keep the system running optimally.
Q4: What is the ideal temperature for chilled water in an HVAC system?
A: The ideal temperature is between 40 to 50°F (4 to 10°C) for efficient operation.
Q5: Can a chilled water system be used for heating?
A: Yes. Heat recovery chillers can be used to cool buildings in the summer and heat them during winter.