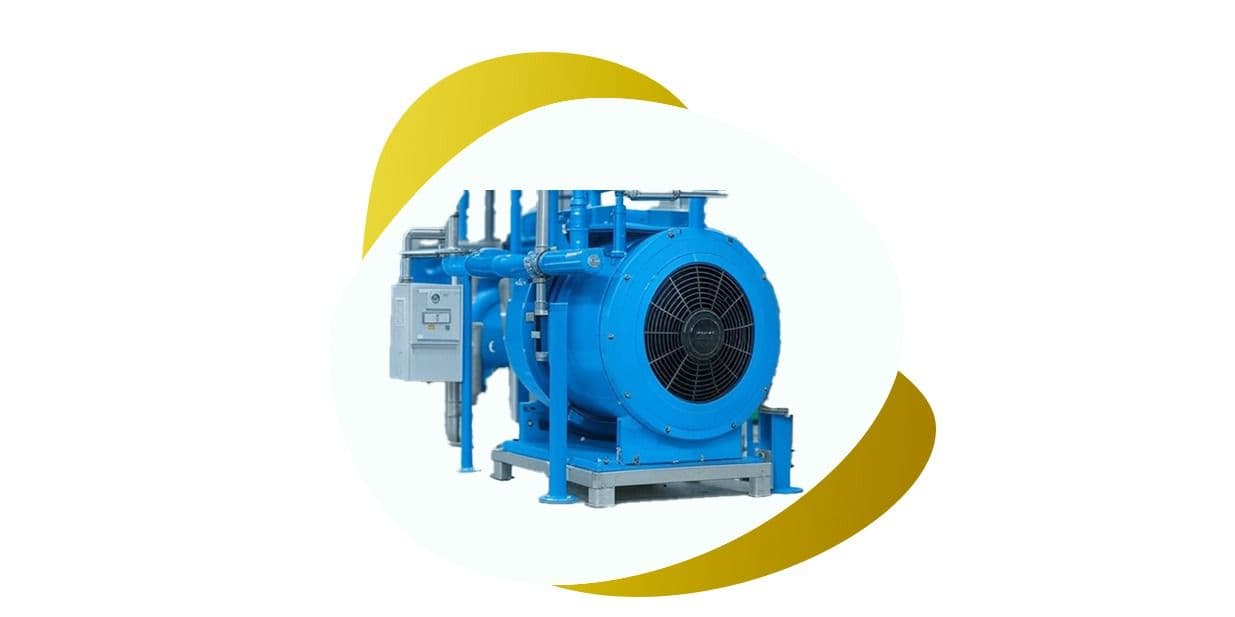
The engineering world depends on centrifugal compressors to fulfill the requirements of aerospace, automotive and power generation fields as well as industrial processing needs. Engine performance and efficiency alongside reliability depends heavily on the aerodynamic design characteristics of these compressors. Multiple years of research progress in CFD with materials science and manufacturing technology have led to enhanced centrifugal compressor designs. Research and innovation needs to continue because various hurdles persist. Engineers and researchers continue to face present-day hurdles in conjunction with recent developments toward improved centrifugal compressor aerodynamics.
Fundamentals of Centrifugal Compressor Aerodynamics
Centrifugal compressors convert kinetic energy into pressure energy through the rotation of an impeller, which imparts velocity to the working fluid. The high-velocity fluid then passes through a diffuser, where it is decelerated, leading to an increase in pressure. The key aerodynamic aspects influencing centrifugal compressor performance include:
- Impeller Design: The shape, size, and number of impeller blades affect the efficiency, pressure rise, and flow stability.
- Diffuser Design: The choice of radial, vaned, or vaneless diffusers impacts pressure recovery and losses.
- Flow Separation and Secondary Flows: Managing flow instabilities is crucial to improving efficiency.
- Tip Clearance Effects: Minimizing tip clearance losses enhances performance.
Advances in Centrifugal Compressor Aerodynamic Design
1. Computational Fluid Dynamics (CFD) and Simulation Tools
Modern CFD tools improve the aerodynamic prediction accuracy for centrifugal compressors during developmental stages. Engineers utilize modern CFD methods to achieve the following three objectives.
Engineers can model complete flow behaviors which include turbulence and unsteady effects together with secondary flow characteristics.
Engineers achieve better blade optimization through combination methods of parametric studies and machine learning algorithms.
The analysis of multiphase flow patterns occurs in both wet gas and supercritical CO2 compressors.
2. Three-Dimensional (3D) Blade Design
3D blade profiles now substitute two-dimensional blade structures because they provide multiple benefits:
The use of 3D design profiles decreases both flow separation occurrences and secondary flow losses.
The precise curvature and stacking techniques enable higher pressure ratio operation.
The strengthening of flow stability results from using 3D blade shaping techniques which regulate stall and instability occurrences.
Performance optimization takes place through blade loading distribution management combined with contour optimization of end-wall geometries.
3. Additive Manufacturing (AM) and Advanced Materials
Through the adoption of additive manufacturing (AM) process in compressor manufacturing industries gain the following benefits:
The technology enables complex designs to produce intricate blades which incorporate internal cooling channels.
AM technology allows the development of lightweight structures using titanium alloys together with composite materials which maintain their structural strength.
The AM technology enables designers to achieve faster prototyping methods allowing them to conduct testing cycles that speed up innovation rates.
The incorporation of advanced resistant materials helps extend the lifespan of compressors and achieves higher operational outcomes.
4. Active Flow Control Techniques
The active flow control (AFC) methods exist for aerodynamics enhancement purposes.
Stability enhancement and flow separation reduction happens through blowing and suction techniques.
Plasma actuators function to decrease air resistance alongside improving blade loading.
Tip Injection and Casing Treatments represent methods that control tip leakage flows and enhance operational range.
The real-time adjustments of AFC methods allow compressors to operate better under changing operating circumstances.
5. Machine Learning and AI-Driven Optimization
AI alongside ML generates revolutionary changes in compressor design optimization through their application. Key benefits include:
The evaluation of extensive design possibilities by AI algorithms occurs with accelerated speed through automated design exploration processes.
ML-based anomaly detection through predictive maintenance protects systems from failure occurrences.
Real-time operation optimization of compressors happens through AI-run control systems that use data-driven performance enhancement.
AI and ML methods work with standard compressor design systems to produce more efficient and stronger centrifugal compressors.
Challenges in Centrifugal Compressor Aerodynamic Design
1. Trade-Off Between Efficiency and Operating Range
A main design difficulty in compressor development consists of simultaneously reaching high operational efficiency along with wide operating range. Compressors featuring high energy efficiency operate with restricted stability areas that make them more prone to surge events and stall conditions. Engineers must carefully balance:
Engineers must optimize blade design angles together with incidence angles in order to minimize operation losses with stable performance.
A design of the diffuser elements must balance optimal pressure recovery against surge margin.
Variable Geometry Mechanisms with adjustable inlet guide vanes operate as an adaptability enhancement measure.
2. Surge and Stall Mitigation
Performance of compressors faces restriction through two detrimental phenomena called surge and stall. Anti-surge plans along with technological solutions help minimize adverse effects on compressor performance.
The suppression of surge attacks involves active surge systems with adjustable valves and bleed valves.
The advancements in tip treatments include both casing treatments with honeycomb seals and recirculation slots.
Machines use artificial intelligence to create superior advanced stall prediction models that predict when stalls will occur in advance.
3. High-Speed Flow and Shock Wave Management
Supersonic flow becomes common in centrifugal compressors during operation at high-pressure ratios.
Pressure differences at high-speed operations increase the amount of entropy generation through shock-induced losses.
Shock waves generate blade vibrations that cause structural fatigue of components.
The heating effect of air during flight affects both material reliability and performance level.
High-speed compressors need optimal blade alignment and shock positioning alongside cooling procedures to reach their design potential.
4. Complex Multi-Phase and Non-Ideal Gas Behavior
Centrifugal compressor systems which manage oil & gas, refrigeration and supercritical CO2 cycles experience the following situations:
Non-Ideal Gas Effects: Deviations from ideal gas behavior impact thermodynamic modeling.
Aerodynamic difficulties occur due to multiphase flow when liquid droplets coexist with gas mixtures.
Condensation and Erosion Issues: Blade degradation due to liquid droplet impact.
Scientific models alongside experimental testing become necessary for dealing with these intricate system issues successfully.
5. Manufacturing Constraints and Cost Considerations
Modern technology advances have not eliminated manufacturing limitations that affect potential aerodynamic designs. Key challenges include:
Expensive materials together with intricate manufacturing processes become necessary factors in designing high-performance systems.
The performance of a design strongly depends on both tolerances and surface roughness deviations from the original specifications.
The promising aspects of additive manufacturing scale poorly to large industrial manufacturing requirements.
Design optimization must happen through an analysis between manufacturing capabilities and economical aspects.
Future Outlook
Aerodynamic design for centrifugal compressors will progress according to these main factors:
Advanced Materials and Coatings: Nano-coatings and shape memory alloys for improved performance and longevity.
The next-generation technology that exists today allows adaptive blade morphing while performing real-time compressor performance adjustments.
Sustainable and Eco-Friendly Designs: Optimization for renewable energy applications, such as hydrogen and carbon capture systems.
Academia and industry should continue working with research institutions to face present difficulties along with unlocking new centrifugal compressor technology applications.
Conclusion
Centrifugal compressors undergo significant aerodynamic development because of improvements in CFD modeling as well as AI-driven optimization and enhanced materials and active flow control systems. The field requires continuing research and development because surge mitigation and high-speed flow losses and multiphase behavior remain as unaddressed challenges. Through the adoption of modern technologies in combination with innovative design methods engineers can improve centrifugal compressor capabilities for industrial and aerospace purposes.