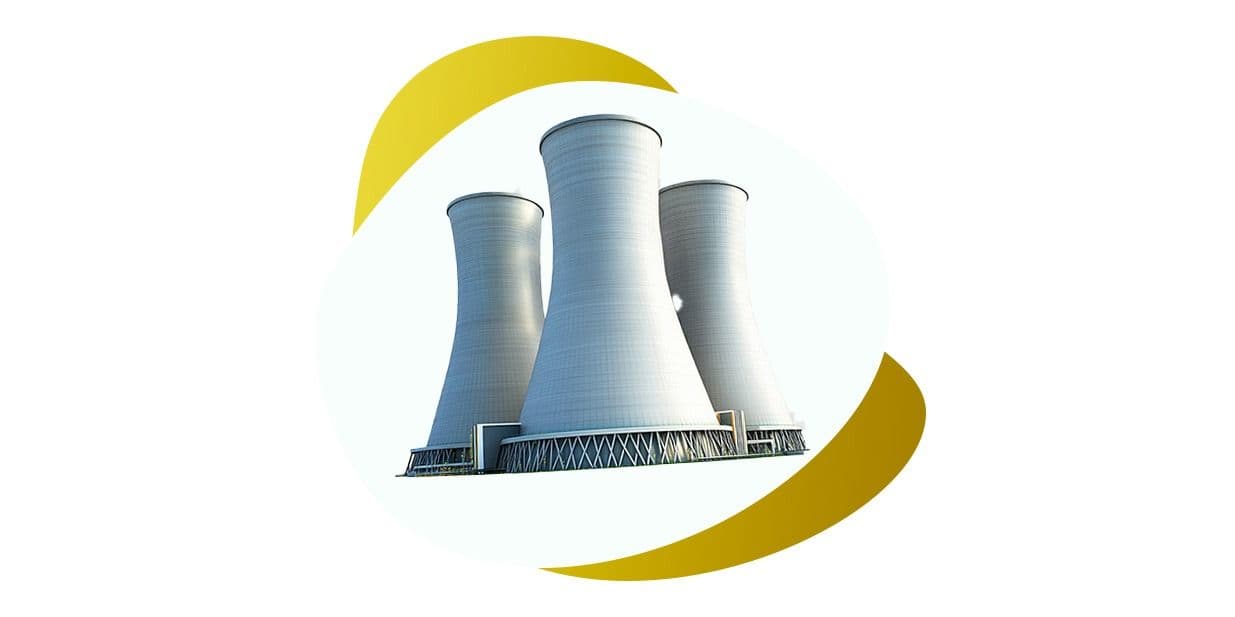
Cooling Towers: An In-Depth Overview
Have you ever wondered how large industrial plants, power stations, and massive buildings regulate temperature efficiently? The answer lies in cooling towers—an essential part of HVAC and industrial cooling systems. These towers play a crucial role in dissipating excess heat, ensuring optimal system performance while conserving energy. In this article, we will explore the types, working mechanisms, advantages, maintenance, and frequently asked questions about cooling towers.
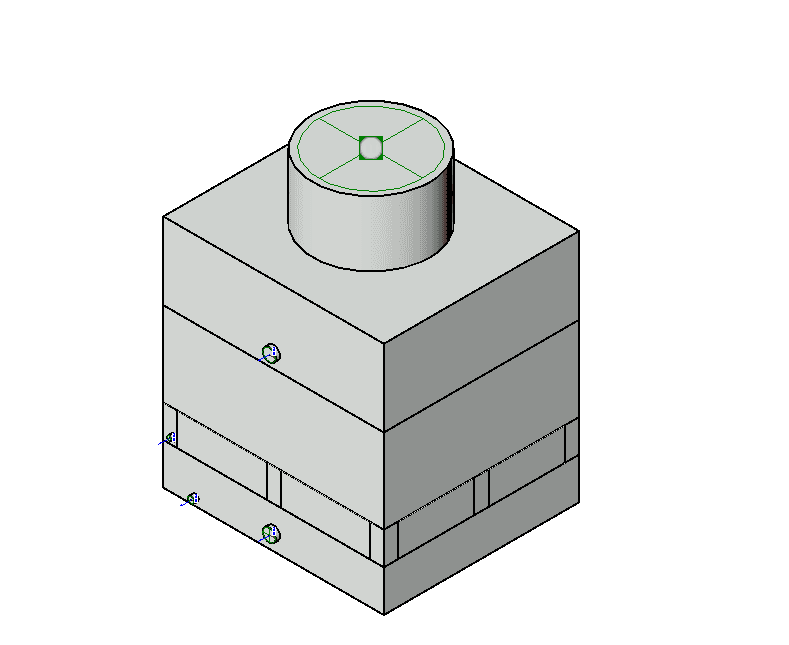
What is a Cooling Tower?
A cooling tower is a specialized heat exchanger that removes waste heat from industrial and commercial processes by utilizing water and air. These systems are widely used in power plants, chemical manufacturing, and large-scale HVAC systems to prevent equipment from overheating.
Cooling towers enhance industrial efficiency by maintaining operational temperatures. Without them, energy consumption would surge, equipment could be damaged, and overall performance would decline.
How Does a Cooling Tower Work?
Cooling towers operate on the principle of heat exchange by evaporative cooling. Here's how the process unfolds:
- Hot Water Entry: Heated water from an industrial process or HVAC system enters the cooling tower through pipes.
- Water Distribution: The water is distributed evenly across the fill media using spray nozzles or splash bars, ensuring maximum exposure to air.
- Airflow Mechanism: Air is drawn into the tower either through natural convection or by mechanical fans.
- In natural draft towers, air moves due to temperature differences.
- In mechanical draft towers, fans enhance air circulation.
- Evaporative Cooling Process: As water droplets interact with the air, a portion of the water evaporates, absorbing heat in the process. This effect significantly lowers the temperature of the remaining water.
- Cooled Water Collection: The cooled water is collected in the basin at the bottom of the tower and recirculated back into the industrial system or HVAC unit.
- Heat Dissipation: The warm, moist air is expelled into the atmosphere, preventing heat buildup within the system.
- Drift Eliminators: These components minimize water loss by capturing small water droplets that could escape with the exhaust air.
- Blowdown System: A portion of the water is periodically discharged to remove accumulated minerals and impurities, preventing scaling and corrosion.
- Temperature Control Sensors: Modern cooling towers include automated sensors that monitor water temperature and adjust airflow or water distribution for optimized performance.
- Water Treatment System: Chemical treatments prevent biological growth and scale buildup, ensuring efficient operation.
Types of Cooling Towers
Cooling towers come in various designs, each tailored for specific applications. Below are the primary types:
1. Natural Draft Cooling Towers
- Utilize natural convection for airflow, eliminating the need for mechanical fans.
- Commonly found in power plants and large-scale industries.
- Require significant space but have low operational costs.
- High initial investment but minimal maintenance needs.
2. Mechanical Draft Cooling Towers
- Use motorized fans to draw or push air for cooling.
- More effective in regions with moderate to high temperatures.
- Further classified into induced draft and forced draft towers.
- Require regular maintenance due to moving components.
3. Crossflow Cooling Towers
- Water moves downward, while air flows horizontally.
- Energy-efficient and cost-effective in large commercial buildings.
- Require effective water management to prevent distribution inefficiencies.
4. Counterflow Cooling Towers
- Air and water flow in opposite directions, improving heat exchange.
- More compact but require higher energy input.
- Offer better thermal efficiency, making them ideal for intensive applications.
5. Closed-Circuit Cooling Towers
- Maintain a closed loop, preventing direct contact between water and air.
- Ideal for systems that require contamination-free cooling.
- Higher initial costs but lower water consumption and scaling issues.
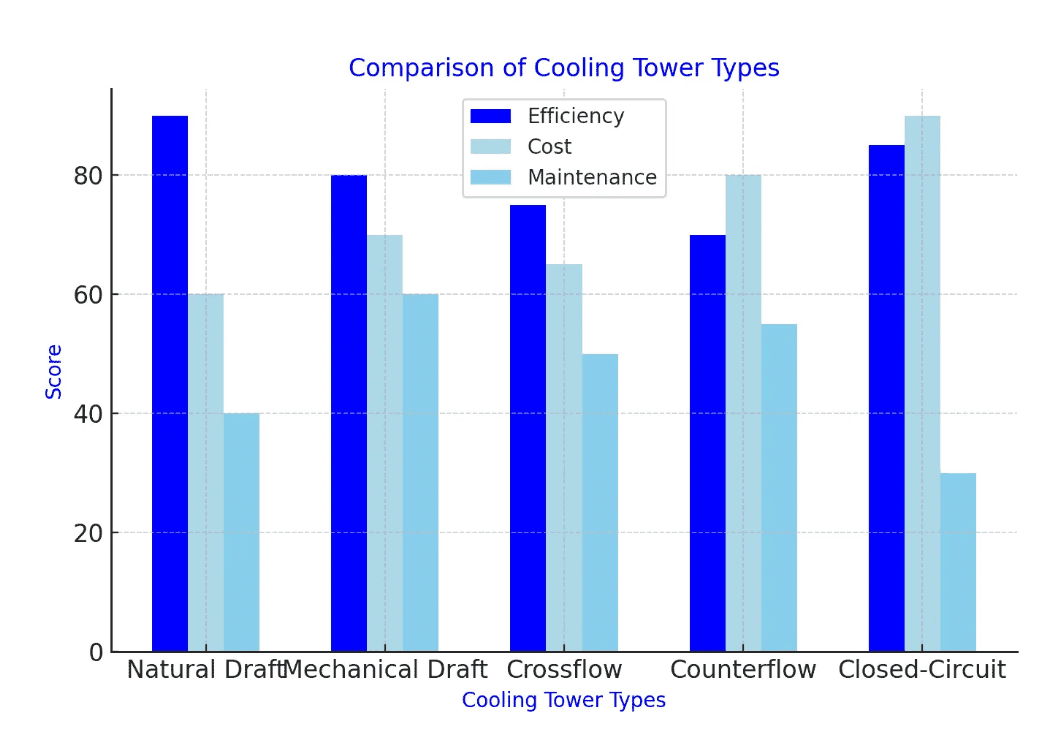
Benefits of Using Cooling Towers
Cooling towers offer multiple advantages, making them essential for industrial and commercial applications:
- Cost Efficiency: Reduces energy expenses compared to conventional cooling systems.
- Environmental Benefits: Lowers carbon footprint through efficient water recycling.
- Affordability: Reduces dependence on costly air conditioning systems.
- Versatility: Can be adapted to different infrastructure sizes and industries.
- Sustainability: With proper upkeep, cooling towers can function efficiently for decades.
- Regulatory Compliance: Advanced water management features help meet strict environmental regulations.
- Improved Equipment Lifespan: Maintains optimal operating temperatures, preventing overheating.
- Scalability: Cooling tower systems can be expanded to accommodate increased operational demands.
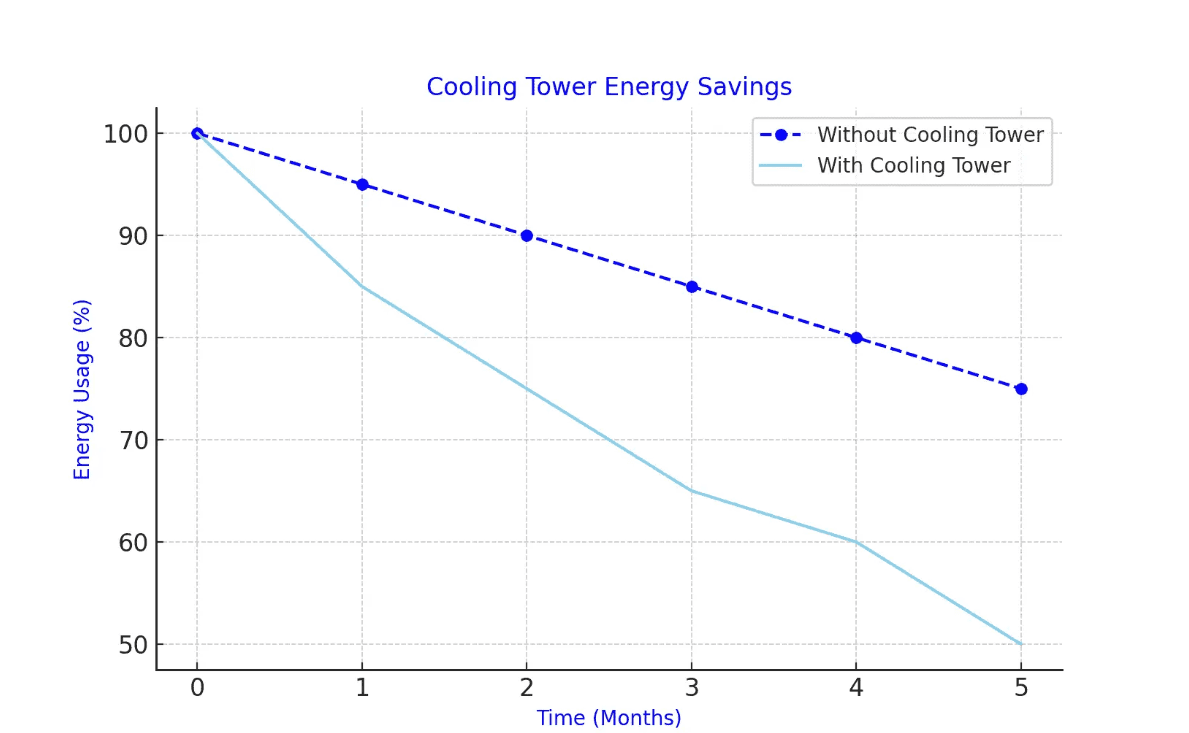
Common Issues and Maintenance Tips
To ensure smooth operation, regular maintenance is crucial. Below are common problems and solutions:
Frequent Issues:
- Scaling and Sediment Build-Up: Prevented through water treatment and descaling agents.
- Microbial Growth: Routine disinfection prevents bacteria such as Legionella.
- Fan Motor Failure: Regular lubrication and inspection prevent mechanical failures.
- Pump Malfunctions: Overheating and poor lubrication can lead to breakdowns; scheduled maintenance is essential.
- Corrosion: Protective coatings help extend the lifespan of metal components.
- Drift Losses: Water droplets escaping into the atmosphere require drift eliminators.
- Clogging of Fill Media: Dust and biological contaminants can block the fill, reducing efficiency.
Maintenance Best Practices:
- Conduct routine cleaning to prevent debris accumulation.
- Use water treatment chemicals to control scaling and microbial contamination.
- Inspect and replace worn-out fan blades, pumps, and critical components.
- Ensure optimal airflow distribution for maximum efficiency.
- Perform regular system diagnostics to detect potential issues early.
- Monitor water quality to reduce fouling and biological contamination.
- Check for structural integrity to prevent unexpected failures.
- Implement automation for real-time monitoring of cooling tower performance.
Understanding Energy Efficiency in Cooling Towers
Cooling towers are essential for dissipating heat in industrial and commercial settings, but they can consume significant energy, especially through fans and pumps. To improve efficiency, consider using VFDs to adjust fan speeds based on demand, which can lower energy use. Regular maintenance, like cleaning to prevent scale and corrosion, helps maintain heat transfer efficiency. Optimizing water temperature and cycles of concentration can also reduce energy needs by minimizing waste.
For example, a case study from an Illinois food service plant showed nearly 60% energy savings after upgrades, including VFDs and free cooling. While these methods are promising, the best approach depends on your specific setup, so consulting a specialist might be helpful.
An unexpected detail is how water treatment, like biocide programs, not only saves energy by preventing fouling but also reduces risks like Legionnaires' disease, linking efficiency to safety.
Cooling Tower Types and Efficiency
Different cooling tower designs, like counterflow and crossflow, impact energy use. Counterflow towers are generally more thermally efficient but may require more fan energy, while crossflow towers use less fan energy but can be less efficient overall. Hybrid towers, combining wet and dry cooling, offer flexibility for energy savings in varying climates, though they can be costlier to install.
Practical Steps for Improvement
- Install VFDs on fans and pumps to adjust speeds dynamically.
- Use free cooling methods, like plate heat exchangers, to leverage cooler ambient conditions.
- Regularly inspect and clean towers to prevent efficiency losses from fouling.
- Maximize cycles of concentration to reduce water and energy waste, typically aiming for six or more cycles where possible.
For more details, check resources like Cooling Tower Efficiency Tips or Energy Savings Case Study.
Comprehensive Analysis of Energy Efficiency in Cooling Towers
Cooling towers are critical components in industrial and commercial facilities, used to dissipate heat through evaporative cooling, thereby supporting processes like HVAC systems, power generation, and manufacturing. Given the rising costs of energy and water, optimizing cooling tower efficiency has become a priority for reducing operational expenses and environmental impact. This note provides a detailed examination of energy efficiency strategies, drawing from recent research, case studies, and best practices, as of March 9, 2025.
Background and Importance
Cooling towers remove heat from water used in chillers, condensers, or process equipment by evaporating a portion of the water, transferring heat to the atmosphere. Energy consumption primarily arises from fans, pumps, and the cooling process itself, making efficiency improvements essential. The focus on energy efficiency aligns with global sustainability goals, such as reducing carbon emissions and conserving resources, while also addressing economic pressures from high energy costs.
Research indicates that cooling towers can be significant energy consumers, with fans and pumps often accounting for a substantial portion of HVAC energy use, as seen in cleanroom facilities where pumps contributed 17-18% of total energy demand (Best Practice for Energy Efficient Cleanrooms). This highlights the need for targeted efficiency measures.
Strategies for Enhancing Energy Efficiency
Several strategies have been identified to improve cooling tower energy efficiency, supported by both theoretical research and practical implementations:
- Variable Frequency Drives (VFDs):
- VFDs allow dynamic adjustment of fan and pump speeds based on cooling demand, reducing energy consumption during low-load periods. A case study from an Illinois food service products manufacturer demonstrated a 37% reduction in base energy use and a 32% reduction in kW per ton after installing VFDs for tower fans and pumps (Cooling System Energy Savings). Further phases, including chiller compressor VFD retrofits, increased total savings to over $340,000 annually, nearly 60% of original energy costs.
- This approach is particularly effective in forced draft towers, where fan energy is a major component, and can be implemented with a relatively low cost and difficulty, as noted in best practices (Cooling Tower Best Practices).
- Free Cooling and Optimized Controls:
- Free cooling leverages ambient conditions, such as cooler nighttime temperatures, using plate heat exchangers to reduce chiller runtime. The Illinois case study showed additional savings of $71,000 per year by integrating free cooling, optimizing tower water setpoint control to balance auxiliary equipment and chiller power (4 Ways to Optimize Cooling Towers).
- Advanced control strategies, like condenser water temperature optimization, ensure the system operates at the most efficient parameters, adjusting based on ambient conditions and load, further enhancing energy savings.
- Maximizing Cycles of Concentration:
- Cycles of concentration measure the increase in total dissolved solids (TDS) in cooling water compared to makeup water. Increasing cycles reduces blowdown, conserving water and energy. Research suggests that increasing from three to six cycles can reduce makeup water by 20% and blowdown by 50%, as highlighted in federal cooling tower management practices (Best Management Practice #10).
- However, there’s a practical limit, typically around seven cycles, beyond which scaling and deposition can reduce efficiency, especially in regions with hard water. Balancing water savings with heat transfer impacts is crucial, often requiring pretreatment of makeup water.
- Regular Maintenance and Cleaning:
- Fouling from scale, biological growth, and corrosion can reduce heat transfer efficiency, increasing energy consumption. Best practices recommend periodic inspections to ensure tower fill media and heat transfer surfaces are clean, potentially improving efficiency by 5% or more (Cooling Tower Best Practices).
- Water treatment programs, including biocides to control bacteria and algae, not only enhance energy efficiency but also mitigate risks like Legionnaires' disease, linking operational efficiency to safety (Energy Savings for Buildings). Routine mechanical cleanings, such as removing debris, are integral to maintaining performance.
- Balanced Water Distribution and Operational Strategies:
- Ensuring even water distribution across the tower prevents hot spots and improves cooling efficiency. Operating multiple towers simultaneously, rather than staging them individually, can be more energy-efficient, especially with VFDs on fans, as suggested in HVAC maintenance best practices (BetterBricks Cooling Tower Maintenance).
- A condenser water reset strategy, setting the leaving water temperature at least 5°F higher than the ambient wet-bulb temperature, optimizes energy use by aligning operation with environmental conditions.
Conclusion
Cooling towers are vital to industrial and commercial cooling solutions, offering significant energy and cost savings. Understanding their types, applications, and maintenance ensures businesses can maximize efficiency while minimizing environmental impact. Investing in well-maintained cooling towers enhances operational reliability and supports sustainable energy practices.
Frequently Asked Questions
1. Where are cooling towers used?
Cooling towers are commonly utilized in commercial buildings, power plants, manufacturing facilities, chemical processing plants, and refineries.
2. How long do cooling towers last?
With proper maintenance, cooling towers typically last between 15 and 25 years.
3. Do cooling towers waste water?
No. Cooling towers recycle most of the water used, though some is lost due to evaporation and blowdown.
4. How can cooling tower efficiency be improved?
- Upgrade fill material for better heat exchange.
- Maintain cleanliness to prevent scaling and microbial growth.
- Optimize fan and pump control for reduced energy consumption.
- Implement automated monitoring systems to track efficiency.
5. Are cooling towers environmentally friendly?
Yes. Compared to conventional cooling systems, cooling towers conserve water, reduce greenhouse gas emissions, and operate using a closed-loop system.